In the early morning hours of March 26, the cargo ship Dali, chartered by Maersk, briefly lost power before it rammed into Baltimore’s Francis Scott Key Bridge. The structure collapsed into the water, resulting in the deaths of six workers completing maintenance of the structure and blocking passage into the Port of Baltimore.
While events disrupting the flow of goods into major ports routinely cause intense and long-lasting supply chain disruptions, and these logistics impacts will receive headlines for days and weeks to come, they are also often tragedies with a significant impact to families and entire communities.
Understanding The Trade Ramifications of the Baltimore Bridge Collapse
Operators at the Port of Baltimore handled $80.8 billion worth of freight in 2023. While that number is dwarfed by other ports in the area, the Port of Baltimore is a major waypoint for regional freight.
While cleanup of the trade lane continues, shipments into the Port of Baltimore have been extremely limited. According to Vizion’s TradeView container shipment data, more than 50 percent of the containerized cargo it tracked that was originally bound for Baltimore has been rerouted to the Port of New York, with 32 percent of the freight heading to the Port of Norfolk. The Port of Philadelphia is set to receive around 12 percent of that freight, with ports in Charleston, Savannah and Boston receiving very slight percentages of diverted cargo.
Vizion is currently tracking a large number of containers that were originally bound for the Port of Baltimore. Not all report a clear destination depending on the carrier or source of their data, and the Vizion team is monitoring the containers to analyze how shipments and routings shift as the Baltimore bridge situation unfolds.
What cargo has been rerouted from the Port of Baltimore?
While the Port of Baltimore isn’t a major U.S. destination for containerized freight, it is a significant port of entry for bulk and tanker commodities and roll on/roll off automobiles. Using data from TradeView, a global trade intelligence platform developed in collaboration with Dun & Bradstreet, Vizion has aggregated the product types and companies most impacted by the Baltimore Bridge Collapse. Using verified, industry-leading datasets from a variety of sources, TradeView builds comprehensive visibility over the product types shipped by particular companies, as well as planned shipments over a 90 day period. The following data is available through Vizion’s public Baltimore Bridge Shipment dashboard, made available to the public as business leaders and supply chain professionals work to navigate the disruption created by the closure of the Port of Baltimore.
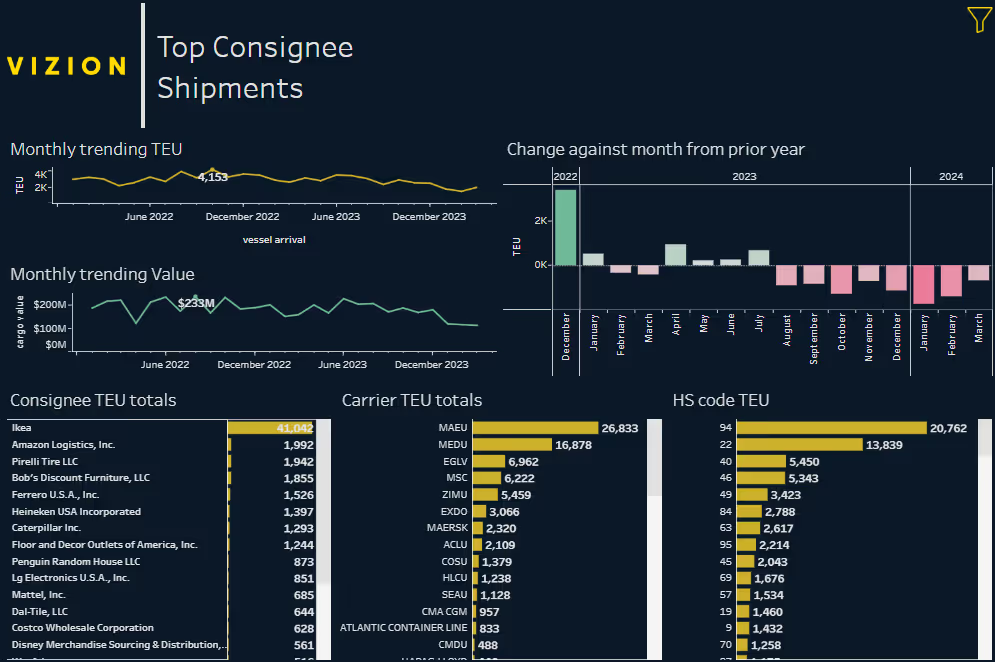
Of shipments identified through TradeView datasets, which cross-reference container codes and shippers to ascertain product types, the containers originally bound for the Port of Baltimore contain goods to be sold by a wide array of retailers. A majority of the freight appears bound for furniture retailers, identified by HS code 94 containers, with Wayfair, Floor and Decor and Bob’s Discount Furniture among the consignees with rerouted cargo. Beverage containers under the HS code 22 designation also saw significant impacts, with shipments from Heineken and Starbucks being greatly impacted by the disruption.
TradeView data reveals that the collapse of the Francis Scott Key bridge has not impacted all retailers equally. Using TradeView, we can better understand the extent of the disruption caused by the closure of the Port of Baltimore. Ikea had been preparing to receive nearly 80 TEU, or twenty-foot equivalent containers, through the Port of Baltimore at the time of the collapse. Historical shipping data from TradeView reveals that Ikea had received nearly 400 TEU with a value of approximately $46M through the Port of Baltimore in March, and was likely ramping down their usage of the port at the time of the collapse.
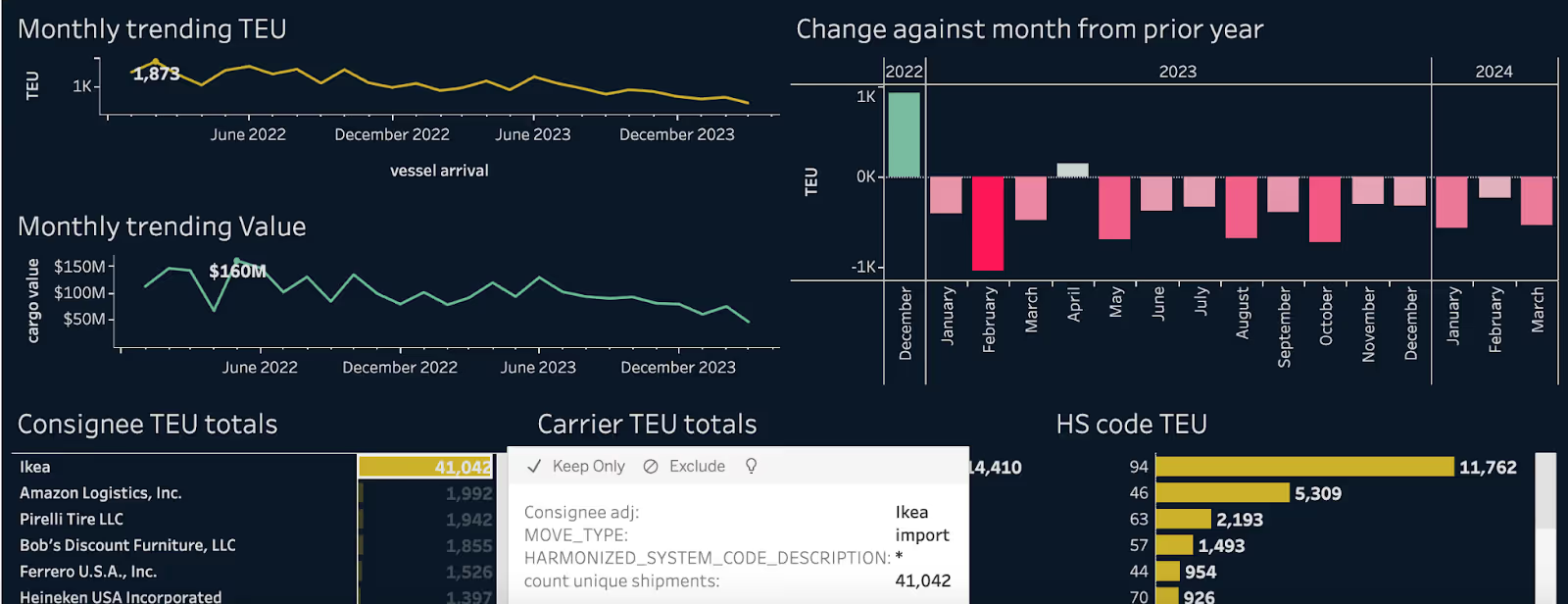
While the significant dropoff in expected volumes reveals that the Swedish furniture retailer was likely planning on moving away from the Port of Baltimore, other retailers and businesses were left with significantly higher volumes inbound at the time of the collapse. Amazon was to receive nearly 2,000 TEU originally destined for the port. Penguin Random House is waiting for, among other cargo, 853 TEU of books and printed material. Staples was set to receive 136 TEU of paper products, 10 TEU of furniture and 2 TEU of books.
Among the retailers hit hardest by the collapse was Bob’s Discount Furniture. The discount furniture retailer had seen low imports in January and February, but, as revealed through TradeView, had been planning on increasing volumes through the Port of Baltimore. In March, the retailer saw some 400 TEU enter the port, and had planned on receiving approximately 200 TEU in the weeks following the collapse.
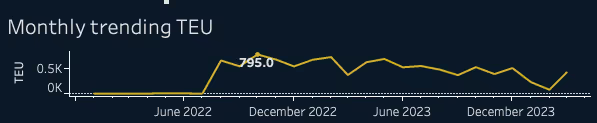
What is the long term impact from the bridge collapse?
While the Port of Baltimore is not a container behemoth like the Port of New York or Los Angeles, the impact upon supply chains will nonetheless be significant and ongoing.
As the largest roll-on, roll-off automotive transportation hub in the country, the port’s closure will undoubtedly impact operations for automotive manufacturers, leading many to divert volumes to nearby ports, such as New York, which is seeing a significant increase in inbound volumes since the collapse. Beyond the automotive sector, experts predict that commodities, such as coal, will see notable impacts. While the Port of Baltimore is generally recognized as an automotive and commodities hub, it also sees significant volumes of cargo related to the food industry, such as coffee and sugar. Stakeholders in these sectors will continue to see longer transportation times as a result of the collapse. Though port authorities have recently opened a small channel into the port for smaller vessels, container ships, which require a significantly larger draft, remain unable to enter the port.
While the impact upon greater supply chain operations will likely be minimal, the impact to local operations will be significant. On average, the bridge played host to roughly 15% of the region’s bridge traffic. While this may not be an especially large portion of the region’s bridge volume, it will nonetheless impact operations for the manufacturing and distribution facilities in the area, including those operated by Amazon, FedEx, and Volkswagen.
In recent days, port officials, alongside the U.S. Army Corp of Engineers (USACE), have announced plans for a staged reopening of the Port of Baltimore. By the end of April, USACE aims to open a 280ft wide, 35ft deep channel that will support one-way barge traffic, as well as some roll-on roll-off vessels. By the end of May, the USACE hopes to reopen the permanent, 700ft wide, 50ft deep channel, effectively reopening the Port of Baltimore to global trade interests.
The Baltimore Bridge Collapse: In the Wake of Catastrophe, Visibility Plays an Essential Role in Resilience and Recovery
When the Dali struck Francis Scott Key Bridge, six families experienced an immense tragedy that makes the impact to the global logistics industry seem small. While any supply chain tangles will be straightened out in the coming weeks, the loss of six workers will reverberate for years to come.
The supply chain impact by the bridge collapse is dynamic but seems relatively limited compared to some of the larger supply chain disruptions experienced in the past few months.
To track the dynamic shifts in the market, shippers use Vizion TradeView for holistic visibility to both macro industry shifts and micro shipment movements. In addition to Vizion’s vessel performance and intelligence data, the TradeView platform utilizes risk and ESG information from Dun & Bradstreet. With it, shippers can track more than $7.5 trillion worth of goods – that’s 60 percent of container shipments worldwide. Traditionally, businesses have used data derived from a variety of sources, the majority of which used Bills of Lading to show shipments already completed, thus allowing visibility exclusively over shipments that have already arrived, and seriously limiting a businesses understanding of competitor inventory movements. Unlike these traditional systems, TradeView is backed by more than 130 different data sources to allow users to monitor both current movements up to 90 days before port arrival and historical shipments for 500 million companies in the global supply chain ecosystem. With TradeView, businesses can maintain constant, real-time visibility over inbound volumes at the nation’s most vital trade hubs.
Book a demo to see how Vizion TradeView empowers you with holistic supply chain visibility.