Poor container visibility can significantly impact a business's financial health, often in ways that aren't immediately apparent. When companies struggle to track the movement and status of their containers, it leads to inefficiencies that can disrupt operations, increase costs, and ultimately decrease profit margins.
Without accurate tracking, businesses may overestimate shipping times or routes, causing unnecessary rerouting or product delivery delayed. The average cost of a supply chain disruption is $1.5 million per day, highlighting the financial strain of inefficiencies.
Delays, mismanagement, and a lack of real-time insights can result in missed opportunities, unexpected expenses, and customer dissatisfaction, all of which contribute directly to the bottom line.
7 Ways in Which Poor Container Visibility Impacts the Bottom Line
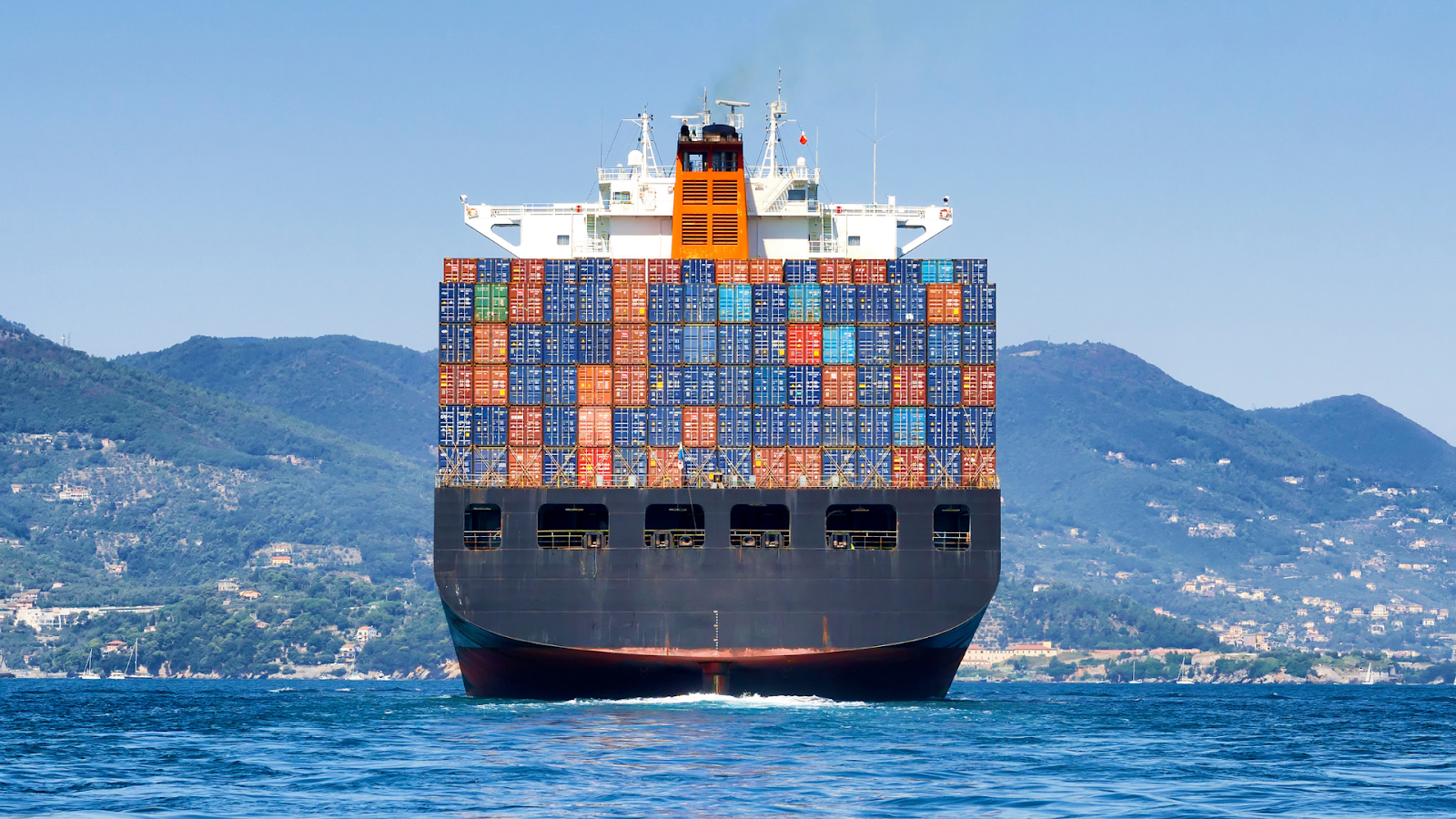
The term bottom line refers to a company's net income or profit, typically shown as the final figure on a financial statement, such as a profit and loss (P&L) statement. It represents the company's overall financial performance after all expenses, taxes, and costs have been deducted from total revenue.
Here's how poor container visibility impacts the bottom line:
1. Higher Operational Costs
Without proper visibility, businesses often rely on manual tracking systems, which require additional labor and administrative overhead. This inefficiency not only increases costs but also creates a blockage in the decision-making process.
Vizion’s real-time tracking and automated data collection eliminate these manual efforts, allowing teams to focus on more strategic tasks and reducing unnecessary operational expenditures.
2. Delivery Delays & Penalties
Missing deadlines and failing to meet customer expectations leads to costly penalties and damaged relationships. These delays also result in higher expedited shipping costs and a loss of trust with customers.
Vizion’s data analytics and real-time updates help businesses proactively address delays before they impact the delivery schedule, minimizing penalties and customer dissatisfaction.
3. Stockouts & Overstocking
Poor visibility causes inaccurate inventory management, often leading to stockouts or overstock situations, which directly affect sales and increase holding costs. Unpredictable inventory levels make it difficult for businesses to plan efficiently and meet demand.
Vizion’s accurate tracking and forecasting capabilities allow businesses to optimize inventory levels, reducing stockouts and overstocking while improving customer satisfaction.
4. Increased Shipping Expenses
Without clear insights into container movement, companies may overestimate shipping times or miss optimal routes, leading to higher fuel costs and unnecessary rerouting. These inefficiencies add up, eating into profit margins.
With Vizion’s real-time container tracking and route optimization, businesses can make smarter decisions that reduce demurrage and detention charges and improve overall supply chain efficiency.
5. Customer Dissatisfaction & Lost Revenue
A lack of visibility into container status frustrates customers, often leading to canceled orders, negative reviews, and loss of repeat business. Delays and poor communication can significantly harm brand loyalty and long-term profitability.
Vizion’s proactive notifications keep customers informed of real-time updates, enhancing transparency and boosting customer retention by providing reliable shipment tracking.
6. Compromised Vendor Relationships
Poor container visibility strains communication with suppliers and logistics partners, causing missed deadlines, errors in delivery schedules, and higher operational costs. This weakens long-term relationships and may even result in vendors seeking more reliable partnerships.
By ensuring clear communication and accurate tracking with Vizion’s smooth integration, businesses can improve vendor collaboration, strengthen partnerships, and reduce inefficiencies.
7. Increased Financial Liability
Inaccurate or outdated tracking makes it challenging to identify issues with damaged or lost shipments, leading to higher insurance claims, costly repairs, or replacement expenses. This can significantly impact a business’s bottom line.
Vizion’s end-to-end visibility and real-time tracking ensure quicker identification of discrepancies, reducing the financial burden of damaged goods and lowering the need for claims.
5 Best Practices for Achieving Optimal Container Visibility with Vizion
Improving container visibility is essential for reducing costs, minimizing delays, and enhancing supply chain efficiency. By implementing key best practices and incorporating Vizion’s advanced tracking solutions, businesses can gain real-time insights, streamline operations, and improve decision-making.
Here are some key strategies for better container visibility:
1. Real-Time Tracking & Automation
Manual tracking is inefficient and prone to errors. Investing in automated tracking solutions like Vizion ensures accurate, real-time updates on container status, location, and estimated arrival times, helping businesses proactively address delays.
2. Easy Integration with Supply Chain Systems
Visibility tools should work effortlessly with TMS and ERP systems to provide a unified view of shipments. Vizion’s API standardizes carrier data, making it easier for businesses to integrate tracking information into their existing platforms.
3. Proactive Alerts & Notifications
Businesses need to act on disruptions before they escalate. Vizion enables automated alerts for shipment delays, transshipments, and estimated arrivals, allowing teams to make quick adjustments and maintain operational efficiency.
4. Data Standardization for Accurate Insights
Consistency in shipment tracking data is critical for making informed decisions. Vizion’s API converts raw carrier data into a structured, standardized format, reducing errors and ensuring supply chain stakeholders have access to reliable information.
5. Scalability for Growing Operations
As shipment volumes increase, businesses need solutions that grow with them. Vizion’s API is designed to scale, ensuring companies maintain visibility across thousands of shipments without manual tracking efforts.
By adopting these best practices and incorporating Vizion’s container tracking technology, businesses can reduce inefficiencies, lower costs, and maintain a competitive edge in global logistics.
Conclusion
The financial impact of poor tracking can be significant, ranging from increased shipping costs and inventory mismanagement to delays and strained vendor relationships. Businesses that invest in real-time visibility solutions can mitigate these risks, optimize their supply chains, and maintain a competitive edge.
Vizion provides a powerful solution by offering automated container tracking, predictive insights, and easy integration with existing logistics systems. By incorporating Vizion’s technology, companies can reduce disruptions, improve decision-making, and ultimately protect their bottom line. In an industry where every delay translates to lost revenue, enhancing container visibility isn’t just an option; it’s necessary for long-term success.
- Real-Time Container Tracking: Gain access to the most complete, standardized, and detailed container tracking events via API or user interface with real-time container tracking data.
- Logistics Performance Hub: Access a comprehensive suite of global logistics datasets, including Port Performance, Port Activity, and Port Pairs, to analyze shipping trends, port throughput, container dwell times, and real-time port activity, enabling smarter decision-making about containerized freight movements.
- TradeView: Monitor the live flow of any company's shipments 30 to 90 days before arrival to destination and analyze trends across 10 years of historical supplier, product, and logistics movement data. With 900 million shipment records, 140+ attributes per shipment, coverage spanning 190 countries, and comprehensive HS code data, TradeView empowers data-driven decisions that optimize global trade management.